How wooden houses can transform Uganda's housing crisis

Wooden houses can position Uganda for a sustainable future by addressing the housing crisis through cost-effective, eco-friendly construction, reducing carbon emissions, and promoting responsible timber sourcing.
Modern wooden construction is revolutionising the housing market as a sustainable and cost-effective alternative to steel and concrete. Not only does it drastically cut construction costs, but it also reduces environmental impact while offering the warmth and aesthetic charm that only natural materials can provide. This has convinced many engineers, architects, and impact investors to consider it a go-to resource to address the housing crises many Ugandans are grappling with, but in a more stylish, sustainable way.
Easy Housing, a real estate developer since 2020, has been leading this charge in Uganda, building homes in 120 days. The company sources its timber from Busoga Forestry Company, which is Forest Stewardship Council-certified, ensuring sustainability.
Before the wood is used, it goes through kiln drying, careful planning, and pressure treatment to keep termites and pests away. The company also skips the concrete jungle and instead uses recycled plastic to craft foundation blocks, lifting its lovely wooden floors by 35 to 80cm. This design promotes air and water flow underneath.
Challenges in the housing market
As many companies venture into this sustainable housing market, we must ask ourselves: where does this timber come from? Urban areas are growing rapidly, leading to a housing deficit of 2.4 million units in Uganda, according to Habitat for Humanity. Other causes of this are the limited land in urban areas and low incomes.
To tackle this, the government has teamed up with private companies, expanding mortgage options and promising to develop infrastructure like roads and utilities in planned estates. These efforts have, however, not solved the problem because of the same reasons that exacerbate the housing deficit, leaving many Ugandans still struggling to find affordable homes.
If wooden homes truly represent the future of housing, as many believe, it’s important to explore how to make this solution sustainable—not just in terms of construction but also regarding responsible sourcing and long-term viability.
Recognising forests as crucial to combating climate change is gaining traction, supported by initiatives like the European Union's Forest Strategy for 2030 and incentive-based legislation in countries such as France but less in developing countries that typically follow suit from the developed nations’ lead.
Currently, the built environment accounts for a staggering 40 percent of global greenhouse gas (GHG) emissions, a figure expected to rise as urban populations continue to swell, according to Climate Group, one of the non-profits driving global climate change solutions. Its data projects the world’s urban population to double by 2050, with nearly 90 percent of that growth occurring in Asia and Africa.
Another anecdotal data point shows that over the last decade, we’ve added more than 50 billion square metres of concrete floor area—an astounding statistic that underscores the urgent need for sustainable building practices. To put that into perspective, that's like building 11 Roman coliseums every half hour. By 2050, that floor space will increase by 70 percent. The problem, however, is that being non-biodegradable, concrete poses waste management challenges because it can take hundreds of years to decompose.
Sustainable sourcing of timber
We have long relied on depleting the Earth's natural resources—cutting down forests and digging up the ground—to build and expand our cities, homes, fuel, and agricultural products, as recent reports have shown, accelerating deforestation at an alarming rate.
“The problem is largely based on the fact that those forests are not valued for their plethora of benefits that they provide—water, clean air, carbon, biodiversity and cultural heritage mostly because none of those can compete with a monetarised value of stolen timber, creating crops, building a new road, or converting for real estate,” said Jamie Lawrence, an impact investor, who is also a co-founder and Forest Strategy Lead at Xilva, a specialised due diligence provider that works to scale global financing opportunities for nature-based solutions.
“But, perhaps, instead of regarding forests as a zero-sum game and construction as simply extractive, to keep carbon out of the atmosphere, many people today are exploring a systemic solution to the use of bio-based materials such as wood in construction. Now, when managed well, forests to frame value chains can offer three interconnected opportunities; to maximise carbon sequestration, storage, and substitution,” he adds.
Sustainability has its roots in forests thanks to Hans Carl von Carlowitz, a German tax accountant from 1713. Concerned about a potential wood shortage for mining, he devised a plan to ensure a steady supply of timber. His ideas laid the foundation for responsible forest management, creating the model we still use today to keep forests sustainable while balancing ecological care with economic needs.
“If you don't value a forest, it gets burnt down or cut down for something immediately more valuable like crops. If you only offer demand for short-lived, fast consumables, you get short rotation and fast-growing species. You get my point. The market has a huge role to play in influencing forest typology and protection,” Mr Lawrence emphasised on Wednesday during an online conference about making forestry sustainable for housing.
“But the use of wood is only a climate solution if the forest carbon sink is intact. Without looking after the forest, you could end up sourcing from deforested areas, whereby the carbon, and indeed the ethical deficit, is simply too large to offer any contribution to climate efforts,” he added.
Trees absorb carbon dioxide as they grow, and when used as timber, they keep that carbon locked in, even after being cut. Unlike steel or concrete, which release a lot of emissions during production, wood not only stores carbon but also helps us avoid using high-carbon materials, making it a win for the environment.
“And we shouldn't really underestimate the scale of this challenge, nor therefore the potential opportunity if we get it right. Every week, 1.5 million people move into urban areas, thousands of which are moving into slums due to a lack of decent and affordable housing. There is an assumption that economic and population growth inevitably leads to environmental and social degradation we seem to have accepted, I'd like to say today. Let’s collectively refuse to accept that future,” Mr Lawrence says.
Imagine three futures for 1.5 million people needing new homes. In the first, they're built with concrete and steel, adding to carbon emissions—this is already happening worldwide, with urban areas the size of Paris popping up every week.
In the second, the homes are made of wood, but it’s irresponsibly sourced, leaving devastated landscapes and stolen land.
Future of timber construction
The third future is different: Homes are built from responsibly managed local forests, upholding environmental and social standards, and storing carbon for over a century. These buildings are designed for longevity and reuse, creating a sustainable, re-greened community.
Bio-based building tools can contribute to the realisation of this vision by verifying sustainable practices; however, as many climate economists point out, in order to fully measure the impacts of climate change and to comprehend our place in the system and take appropriate action, we still need better science-to-application tools.
“So where are you along this chain? Are you closer to the city, closer to the forest? Understanding where you sit also informs you as to what sort of information you need upstream; like who am I going to for the information about my forest and what is my sphere of influence?” Mr Lawrence rhetorically asks, adding, “The other is to learn from others. There are actually a lot of examples of what can be considered climate-smart value chains around the world.”
Take, for one, Portland Airport in the US. It features timber sourced from well-managed tribal forests. The carbon contribution of these forests was meticulously assessed using a framework developed with architects, helping to secure the winning bid for the project.
“So work with others and understand from others how to replicate those. Many of these examples go from small communities working in very simple value chains to larger commercial enterprises working across complex value chains. So we know it can be done at different scales as well,” he adds.
This poses a challenge, as entrepreneurs tend to avoid working with small-scale timber suppliers operating in isolation. Wolf Bierens, an environmental technology expert and impact entrepreneur specializing in the circular economy and bio-based construction, explains that sourcing from smaller growers can be particularly difficult.
This is because high-quality timber construction requires not just logs but also an entire value chain of processing that occurs after forest harvesting, which is uncommon in East Africa.
“It's not only the sawmill, but it's also the pressure treatment for durability and termite resistance. It's planning, it's profiling. So only a few players in Uganda actually have this. And those that do have, we request quotations to see which are most favourable for procurements. But indeed, for us, the most important part is, 'Can the supplier give us the quality we need, and can they assure the sustainability of their forestry?'” Bierens puts it.
Certification, traceability
The aspect of traceability is vitally important. Mr Lawrence pointed out that knowing where your wood comes from is the first step towards comprehending the carbon footprint of timber and its significance for the climate.
Fortunately, in response to regulations like the European Timber Regulation and the Lacey Act, numerous off-the-shelf solutions are now available to help companies trace timber back down the supply chain. Options include DNA testing to trace the wood back to its origin, cloud-based compliance platforms for information sharing, government-sponsored timber traceability systems, and even QR codes. No matter the method, tracking the origin of timber is now a practical reality.
Uganda currently lacks a standard for "legal timber." Legal timber is generally understood to be wood harvested and traded according to forestry laws and regulations. However, many environmental economists argue that these laws are not clear enough.
“I would be remiss if I didn't mention the possibility and the need for due diligence recognising that this is not only about carbon, it's not a climate solution if it's inequitable, if a local population has been removed from the site to get the timber, or if the biodiversity has been so negatively impacted,” Mr Lawrence says.
Today, you can effortlessly evaluate the health of your forest and its surrounding issues from the comfort of your desk. Certification standards like the Forest Stewardship Council (FSC) can guide you in this process. For long-term supply relationships, it’s crucial to conduct due diligence to identify risks and maximise impact returns.
Fortunately, numerous platforms are at your disposal, such as Global Forest Watch for tracking deforestation rates and the Integrated Biodiversity Assessment Tool for assessing biodiversity.
“And especially if you're making a carbon claim, you really need to model and understand the carbon story of your value chain and that must be appropriate to the claim you're making. Now, in order to do that, we really need to develop tools that can be applied,” Mr Lawrence says.
The Climate Smart Forest Economy Program (CSFEP) developed an approach that tested early versions of the tool for measuring and influencing the various climate functions across the three areas of sequestration, sink, storage, and substitution,” he adds.
But to gain market adoption, these tools for tracking carbon impact in construction must be user-friendly. While many methodologies exist, like the International Organization for Standardisation, Vera, Tosia by Efi, and tools from EC3 or Athena, they don’t yet offer complete, easy-to-use solutions for architects or construction firms.
To be effective, these tools need to account for every project phase, including the end-of-life stages. Some examples, like Easy Housing’s 'Climate Cleanup,' aim to simplify this, but the challenge remains in creating a seamless, practical way to track construction’s stored carbon across the entire value chain.
“This field still needs further development to be more frequently and consistently used. But the true value might not lie in just making carbon claims—it’s in using it as a decision-making tool. In projects like CSFEP, understanding carbon flows helped teams make smarter choices: sourcing from better forests, reducing waste, or adjusting transport routes. So, it’s not just about proving you’re climate-smart, it’s about improving the whole value chain and even benefiting the forests themselves,” Mr Lawrence opines.
Because for one thing, timber is an enabler of climate change. Mr Bierens, who is also the founder of Easy Housing, explains that timber stores about 1,000 kg of CO₂ per cubic metre of timber and stresses that bio-based construction is not only sustainable but also scalable.
“If you look at the combined effects of avoiding carbon by not using either cement or burnt bricks plus the amount of carbon stored in the structure, the amount of carbon storage is between ten and 15 tonnes for an average home. And the carbon substituted or the carbon avoided is also around 10 tonnes of CO₂ when you compare a 100 square metre home with when it would have been built with brick and mortar or concrete, for example,” he says.
Funding the ecosystem
Many industry players believe that investment in the forestry sector is needed because this is the pinnacle that lays the foundation for the forest economy. They nonetheless acknowledge difficulties in the undertaking if anything because there’s not enough demand for their products.
Mr Bierens says from anecdotal evidence he has heard, any forestry company in sub-Saharan Africa, is struggling to financially make ends meet, especially the FSC-certified ones.
In the Democratic Republic of the Congo, for example, there were three big ones, but two had to close down because there was not enough demand for it, especially as compared to, unfortunately, illegal logging, which is taken up on the black market.
“So these FSC-certified companies are only exporting to Europe and abroad. And then in case something happens, it just doesn't work out, even if there are strong international investors behind them,” he says.
“We know that a few weeks ago there was a big pledge for a few hundred million dollars into a forestry fund, of which a part is also moving into the East African forestry sector. But I think it's also difficult to allocate these large institutional chunks of investment in the right way. Like where do you put it and how do you make sure that because on the one hand, you want to stimulate maybe small skill forestry as well. On the other hand, like moving up fast, it's very difficult to find the right players on the ground, I believe,” he adds.
Many industry players in this space, even the investment firms in commercial forestry have made significant investments in growing trees and establishing timber production and processing facilities that are now facing the challenge of demonstrating profitable returns on those investments as their trees mature and are ready for harvest.
Mr Aman Choda, a senior programme manager in the commercial forestry sector for Gatsby Africa, a funder implementer working to help several industries, including commercial forestry, reach their full potential in East Africa, says there is need for resources that suit smallholder growers so that they don’t need to lend themselves to structural timber.
“I do think that in order to see investment flowing in, those firms do need to achieve profits. And the best way to do that is to have a consistent, robust market that offers attractive prices,” he says.
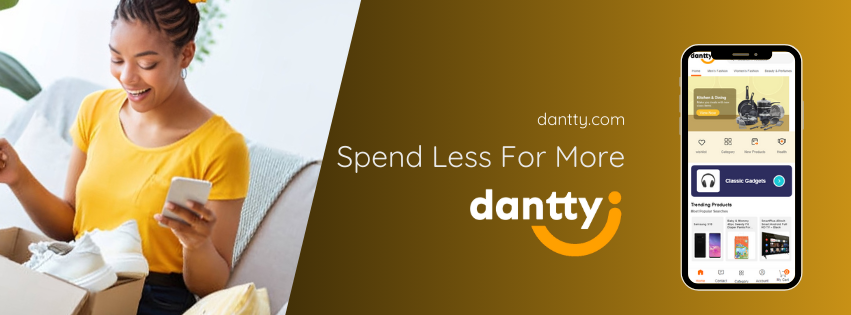
0 Comments